Porosity in Welding: Identifying Common Issues and Implementing Finest Practices for Avoidance
Porosity in welding is a pervasive concern that usually goes unnoticed up until it triggers considerable troubles with the integrity of welds. In this conversation, we will explore the crucial elements adding to porosity formation, examine its harmful impacts on weld performance, and go over the finest practices that can be taken on to decrease porosity event in welding processes.
Typical Causes of Porosity
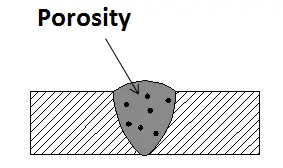
Making use of dirty or damp filler materials can introduce contaminations into the weld, contributing to porosity concerns. To mitigate these typical causes of porosity, comprehensive cleaning of base steels, appropriate protecting gas choice, and adherence to ideal welding parameters are crucial techniques in accomplishing high-quality, porosity-free welds.
Impact of Porosity on Weld High Quality

The existence of porosity in welding can dramatically endanger the structural honesty and mechanical homes of welded joints. Porosity produces voids within the weld steel, compromising its general stamina and load-bearing capability. These voids serve as tension focus factors, making the weld a lot more susceptible to cracking and failure under applied loads. In addition, porosity can reduce the weld's resistance to deterioration and various other environmental aspects, further decreasing its longevity and performance.
One of the primary repercussions of porosity is a decrease in the weld's ductility and durability. Welds with high porosity levels have a tendency to show lower effect toughness and minimized capability to warp plastically prior to fracturing. This can be especially worrying in applications where the find more bonded components undergo vibrant or cyclic loading conditions. Moreover, porosity can impede the weld's capacity to successfully transmit pressures, leading to early weld failing and prospective safety and security dangers in critical structures.
Ideal Practices for Porosity Prevention
To boost the structural stability and quality of bonded joints, what specific measures can be executed to reduce the event of porosity during the welding process? Utilizing the proper welding technique for the certain material being welded, such as changing the welding angle and gun position, can additionally avoid porosity. Normal inspection of welds and prompt removal of any issues recognized throughout the welding procedure are vital methods to stop porosity and produce high-quality welds.
Value of Appropriate Welding Techniques
Implementing appropriate welding techniques is vital in ensuring the architectural stability and high quality of bonded joints, building upon the foundation of effective porosity prevention steps. Excessive heat can lead to increased porosity due to the entrapment of gases in the weld swimming pool. Furthermore, utilizing the proper welding specifications, such as voltage, present, and travel rate, is check critical for achieving audio welds with very little porosity.
Moreover, the choice of welding procedure, whether it be MIG, TIG, or stick welding, must line up with the details requirements of the task to ensure optimal outcomes. Correct cleaning and prep work of the base steel, as well as choosing the appropriate filler product, are likewise necessary components of efficient welding strategies. By adhering to these best methods, welders can decrease the danger of porosity formation and generate top notch, structurally sound welds.

Examining and Quality Assurance Procedures
Checking treatments are vital to detect and avoid porosity in welding, guaranteeing the stamina and durability of the final item. Non-destructive testing approaches such as ultrasonic testing, radiographic testing, and visual inspection are commonly utilized to determine possible flaws like porosity.
Post-weld inspections, on the various other hand, evaluate the final weld for any kind of flaws, including porosity, and confirm that it meets defined criteria. Implementing an extensive top quality control strategy that includes detailed screening treatments and assessments is my website vital to decreasing porosity issues and ensuring the total high quality of bonded joints.
Final Thought
In final thought, porosity in welding can be a common concern that influences the top quality of welds. By determining the typical reasons for porosity and executing finest methods for prevention, such as appropriate welding techniques and screening steps, welders can make certain high top quality and trustworthy welds. It is vital to focus on prevention techniques to reduce the event of porosity and keep the honesty of bonded structures.